Understanding the importance of proper electrical labeling
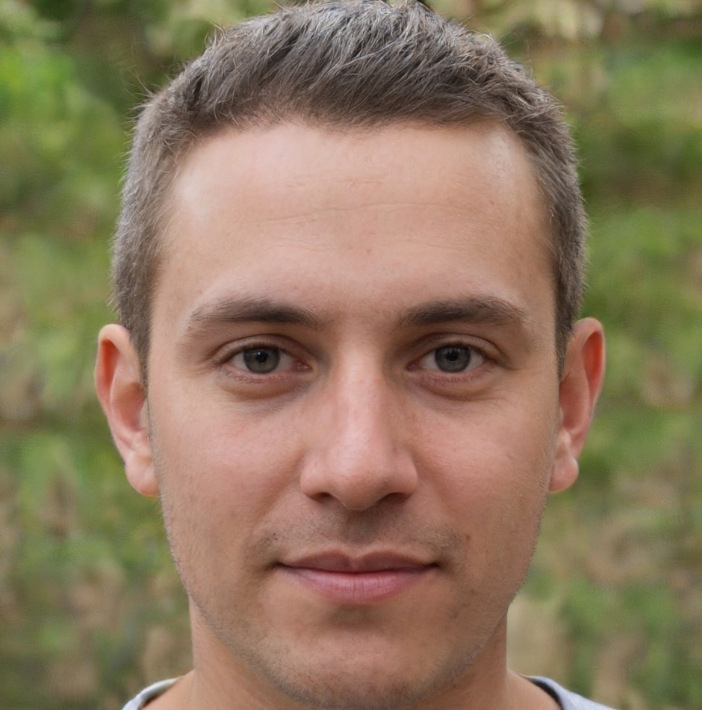

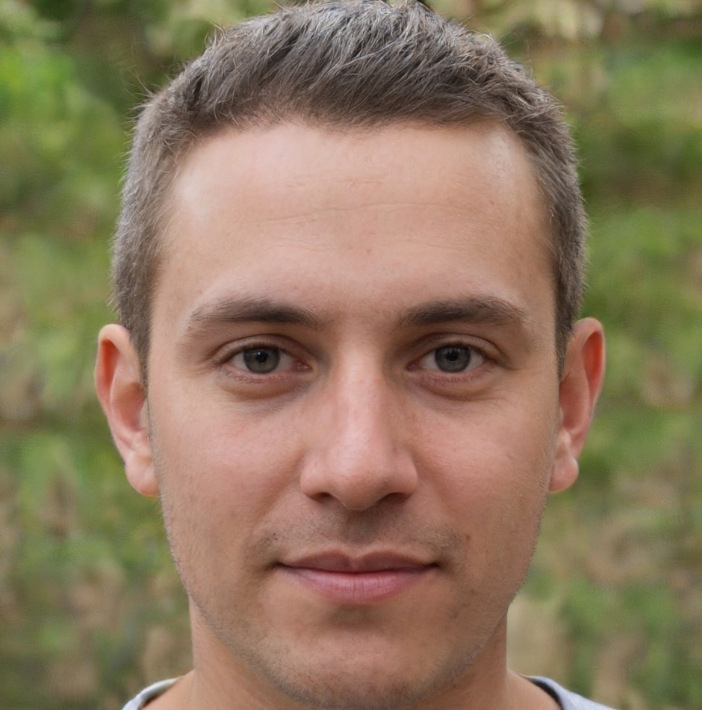
The Power of Clarity: Understanding the Importance of Proper Electrical Labeling
Electrical systems are the backbone of modern infrastructure, powering everything from homes and businesses to industries and transportation systems. With the increasing complexity of electrical networks, the need for clear and accurate labeling has become more critical than ever. Proper electrical labeling is essential for ensuring the safety, efficiency, and reliability of electrical systems. In this article, we'll explore the importance of proper electrical labeling, its benefits, and best practices for implementing an effective labeling system.
The Consequences of Poor Labeling
Poor electrical labeling can have severe consequences, including:
- Accidents and Injuries: Misidentified wires or components can lead to electrical shocks, fires, or explosions, resulting in injuries or fatalities.
- Downtime and Loss of Productivity: Incorrect labeling can cause confusion, leading to unnecessary downtime, and loss of productivity, resulting in significant financial losses.
- Equipment Damage: Mislabeling can result in incorrect installation, maintenance, or repair, leading to equipment damage or failure.
- Non-Compliance: Failure to comply with electrical labeling standards can result in fines, penalties, or even legal action.
The Benefits of Proper Labeling
Proper electrical labeling offers numerous benefits, including:
- Improved Safety: Clear and accurate labeling helps to prevent accidents and ensures a safe working environment.
- Increased Efficiency: Proper labeling enables quick and easy identification of components, reducing downtime and increasing productivity.
- Reduced Errors: Accurate labeling minimizes the risk of human error, ensuring that components are installed, maintained, and repaired correctly.
- Compliance: Proper labeling ensures compliance with relevant standards and regulations, avoiding fines and penalties.
Best Practices for Electrical Labeling
Implementing an effective electrical labeling system requires careful planning and attention to detail. Here are some best practices to follow:
- Use Standardized Labels: Use standardized labels and symbols to ensure consistency and clarity.
- Label Everything: Label every component, including wires, cables, circuit breakers, and electrical panels.
- Use Clear and Concise Text: Use clear, concise, and easy-to-understand text on labels.
- Use Color-Coding: Use color-coding to categorize and differentiate between different types of components or systems.
- Keep Labels Up-to-Date: Regularly update labels to reflect changes to the electrical system or component modifications.
Technologies and Tools for Electrical Labeling
Advancements in technology have made it easier to implement and maintain effective electrical labeling systems. Some of the technologies and tools available include:
- Labeling Software: Specialized software can help design, print, and manage electrical labels, ensuring consistency and accuracy.
- Barcode Scanning: Barcode scanning can be used to quickly and accurately identify components and track inventory.
- Mobile Apps: Mobile apps can provide access to electrical labeling databases, enabling technicians to access information on-site.
- Label Printers: Thermal label printers can produce high-quality labels quickly and efficiently.
Case Study: Effective Electrical Labeling in Practice
A recent study by the National Electrical Contractors Association (NECA) highlighted the importance of proper electrical labeling in the construction industry. The study found that:
- 83% of electrical contractors reported that proper labeling improved job site safety.
- 75% of contractors reported that proper labeling reduced errors and downtime.
- 90% of contractors reported that proper labeling improved overall project efficiency.
In one notable example, a large construction firm implemented a comprehensive electrical labeling system on a multi-million-dollar project. The result was a 30% reduction in downtime and a 25% increase in productivity.
Understanding the Importance of Proper Electrical Labeling
Electrical labeling is a crucial aspect of electrical safety that is often overlooked or underestimated. However, the significance of proper labeling cannot be overstated. It is essential to ensure the safety of individuals, equipment, and facilities, and to prevent electrical hazards that can lead to fatalities, injuries, and property damage.
Electrical labeling is more than just a compliance issue; it is an integral part of electrical safety. Proper labeling helps identify electrical circuits, components, and equipment, enabling electricians and maintenance personnel to perform their tasks efficiently and safely.
Benefits of Proper Electrical Labeling
Improved Safety
Proper electrical labeling is essential for safety. It helps prevent electrical shock, electrocution, and other hazards by ensuring that individuals are aware of the electrical systems and components they are working with. Clear and accurate labeling helps electricians and maintenance personnel identify live wires, energized circuits, and potential hazards, enabling them to take necessary precautions to avoid accidents.
Reduced Downtime and Increased Productivity
Electrical labeling can significantly reduce downtime and increase productivity. When electrical equipment and circuits are properly labeled, maintenance personnel can quickly identify and troubleshoot issues, reducing the time spent on repair and maintenance. This, in turn, leads to increased productivity, reduced costs, and improved overall efficiency.
Compliance and Regulatory Adherence
Proper electrical labeling is essential for compliance with regulatory requirements and industry standards. In the United States, for example, the Occupational Safety and Health Administration (OSHA) and the National Electric Code (NEC) require electrical labeling to ensure electrical safety. Failure to comply with these regulations can result in fines, penalties, and even legal action.
Enhanced Asset Management
Electrical labeling can help enhance asset management by providing valuable information about electrical equipment and systems. Proper labeling enables facility managers and maintenance personnel to track equipment performance, maintenance history, and replacement schedules, leading to improved asset management and extended equipment lifespan.
Consequences of Neglecting Electrical Labeling
Neglecting electrical labeling can have severe consequences, including:
Electrical Accidents and Fatalities
Electrical accidents and fatalities can occur when individuals are unaware of electrical hazards or are unable to identify live wires and energized circuits. According to the International Association of Electrical Inspectors, electrical accidents and fatalities are often caused by inadequate or missing electrical labeling.
Equipment Damage and Property Loss
Inadequate labeling can lead to equipment damage and property loss. When electrical equipment is not properly labeled, maintenance personnel may not be aware of electrical hazards, leading to equipment damage or property loss.
Downtime and Productivity Loss
Neglecting electrical labeling can lead to extended downtime and productivity loss. When electrical issues arise, and equipment is not properly labeled, maintenance personnel may spend hours troubleshooting and repairing, leading to significant productivity losses.
Compliance Issues and Fines
Failure to comply with electrical labeling regulations can result in fines, penalties, and legal action. Organizations may face significant financial losses, reputation damage, and even criminal charges for neglecting electrical labeling.
Best Practices for Electrical Labeling
To ensure proper electrical labeling, organizations should follow best practices, including:
Use Clear and Consistent Labeling
Electrical labels should be clear, concise, and consistent throughout the facility. Labels should include essential information, such as circuit identification, voltage, and ampere ratings.
Use Standardized Labeling Systems
Organizations should use standardized labeling systems, such as the NFPA 79 or the IEEE 1242, to ensure consistency and clarity.
Regularly Inspect and Update Labels
Electrical labels should be regularly inspected and updated to ensure accuracy and relevance. This includes updating labels after maintenance, repairs, or modifications.
Train Personnel on Labeling Systems
Organizations should provide training on electrical labeling systems to ensure that electricians and maintenance personnel understand the labeling system and can use it effectively.
Use Durable and Weather-Resistant Labels
Labels should be durable and weather-resistant to withstand environmental conditions, such as temperature fluctuations, humidity, and exposure to chemicals.
Conclusion
In conclusion, proper electrical labeling is a critical aspect of electrical safety, maintenance, and operation. It is essential to recognize the importance of electrical labeling beyond mere compliance and to understand its benefits and consequences. By following best practices and implementing a standardized labeling system, organizations can reduce electrical hazards, improve safety, and enhance asset management. Remember, electrical labeling is not just a compliance issue; it is a critical component of electrical safety and efficiency.