Wiring Methods for Industrial Facilities
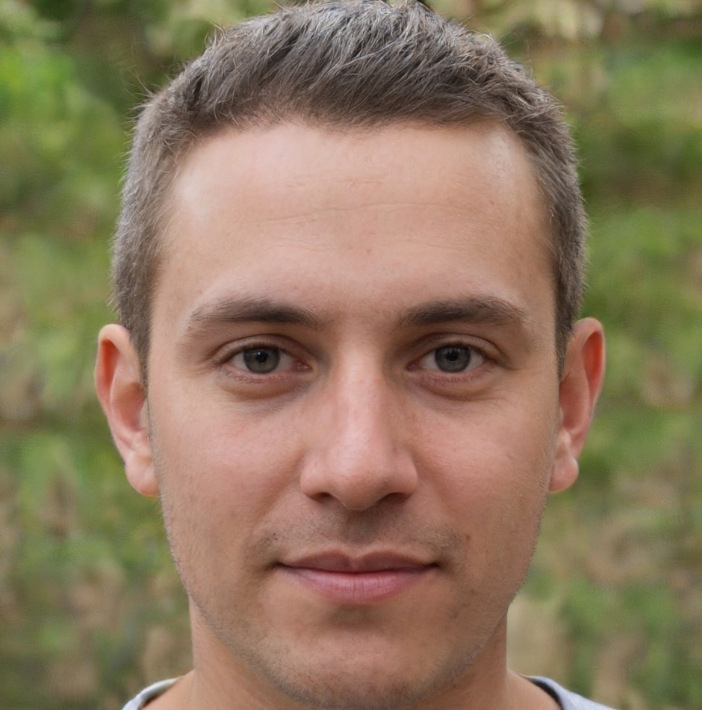

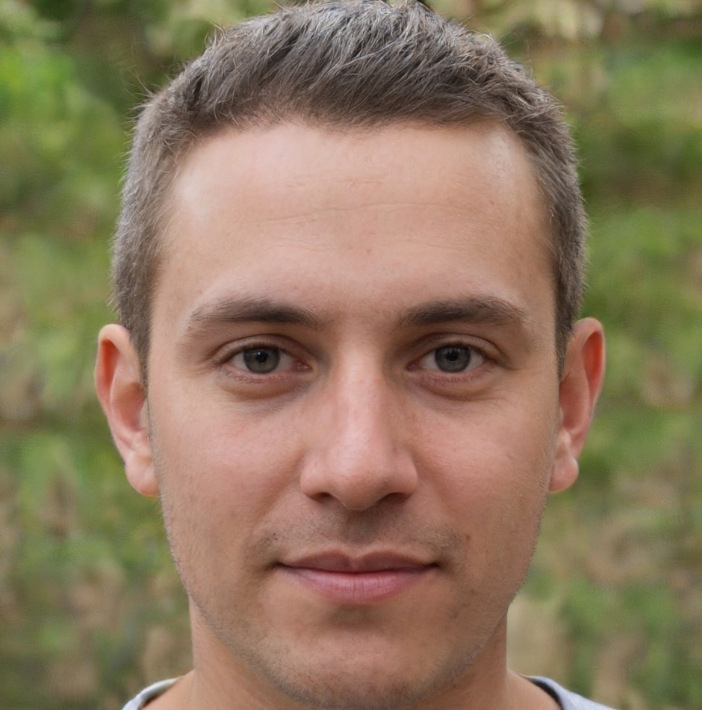
Introduction to Wiring Methods for Industrial Facilities
Wiring methods for industrial facilities are crucial for ensuring the safe and efficient operation of equipment and machinery. Industrial facilities, such as manufacturing plants, power plants, and chemical processing facilities, require a high level of reliability and safety in their electrical wiring systems. The wiring method used can significantly impact the performance and lifespan of the facility's electrical systems. For instance, a facilty with a poorly designed wiring system may experiance alot of downtime due to electrical failures, which can be extreemly costly.
Overview of Wiring Methods
There are several wiring methods that can be used in industrial facilities, including conduit and cable, busways, and cable trays. Each method has its own advantages and disadvantages, and the choice of which method to use depends on the specific requirements of the facility. Conduit and cable wiring is a traditional method that involves threading cables through metal or plastic conduit. This method provides excellent protection for the cables and is suitable for use in harsh environments. Busways, on the other hand, are pre-fabricated wiring systems that consist of a busbar and associated fittings. They are often used in areas where flexibility and ease of installation are important. Cable trays are used to support and route cables in a neat and organized manner, and are commonly used in areas where cables need to be frequently accessed or modified.
Conduit and Cable Wiring
Conduit and cable wiring is a widely used method in industrial facilities due to its high level of protection and flexibility. The conduit provides a rugged and durable barrier against environmental factors such as moisture, chemicals, and extreme temperatures. The cables are threaded through the conduit, which helps to prevent damage from abrasion, compression, and tension. There are several types of conduit available, including rigid metal conduit (RMC), intermediate metal conduit (IMC), and electrical metal tubing (EMT). RMC is the most robust and is often used in areas where high levels of mechanical protection are required. IMC is a thinner and more flexible version of RMC, and is often used in areas where space is limited. EMT is a thinner and more lightweight version of IMC, and is often used in areas where flexibility and ease of installation are important. It's worth noting that the instalation of conduit and cable wiring can be a complex and labour-intensive proces, requiering a high level of skill and expertise.
Busways
Busways are pre-fabricated wiring systems that consist of a busbar and associated fittings. They are often used in industrial facilities due to their flexibility and ease of installation. Busways are available in a range of sizes and configurations, and can be used to distribute power to equipment and systems throughout the facility. They are particularly well-suited for use in areas where high levels of power are required, such as in motor control centers or distribution panels. Busways can be installed quickly and easily, and can be modified or expanded as needed. This makes them a popular choice for facilities that need to be able to adapt quickly to changing circumstances. For example, a facility that is undergoing a major renovation may choose to use busways in order to be able to easily reconfigure the wiring system as needed.
Cable Trays
Cable trays are used to support and route cables in a neat and organized manner. They are commonly used in areas where cables need to be frequently accessed or modified, such as in control rooms or distribution panels. Cable trays are available in a range of sizes and materials, including steel, aluminum, and fiber-reinforced polymer (FRP). They can be installed quickly and easily, and can be modified or expanded as needed. Cable trays offer several advantages over other wiring methods, including reduced installation time and cost, increased flexibility, and improved safety. They are also more environmentally friendly than other wiring methods, as they reduce the amount of materials required for installation. However, cable trays may not be suitable for use in all areas of the facility, such as in areas with high levels of moisture or chemicals.
Cable Management
Cable management is an essential aspect of wiring methods for industrial facilities. It involves the use of various devices and systems to manage and organize cables, such as cable ties, cable clips, and cable trays. Cable management helps to prevent damage to cables, reduce installation time and cost, and improve safety. It also helps to improve the appearance of the facility, which can be an important consideration for facilities that are open to the public or have a high level of visibility. There are several best practices for cable management, including the use of standardized cable labeling and identification, the use of cable ties and clips to secure cables, and the use of cable trays and other cable management systems to route and support cables. Cable management should be an ongoing process, with regular inspections and maintenance to ensure that cables are properly managed and organized.
Case Study: Industrial Facility Wiring Upgrade
A large industrial facility in the United States recently underwent a major wiring upgrade to improve the reliability and efficiency of its electrical systems. The facility, which produces chemicals and pharmaceuticals, had experienced several power outages and equipment failures in recent years due to inadequate wiring. The facility's management team decided to upgrade the wiring to a modern conduit and cable system, which would provide improved protection and flexibility. The upgrade involved the installation of several miles of conduit and cable, as well as the replacement of outdated electrical equipment. The project was completed on time and within budget, and has resulted in significant improvements in the facility's electrical systems. The new wiring system has reduced power outages and equipment failures, and has improved the overall reliability and efficiency of the facility.
Maintenance and Inspection
Regular maintenance and inspection of wiring systems is essential to ensure the safe and efficient operation of industrial facilities. This involves the use of various techniques and tools, such as thermal imaging and electrical testing, to identify potential problems and prevent equipment failures. Maintenance and inspection should be performed regularly, such as every 6-12 months, depending on the specific requirements of the facility. There are several best practices for maintenance and inspection, including the use of standardized maintenance schedules and procedures, the use of trained and qualified personnel, and the use of specialized equipment and tools. Maintenance and inspection should be an ongoing process, with regular reviews and updates to ensure that the facility's wiring systems are operating safely and efficiently.
Best Practices for Wiring Methods
There are several best practices for wiring methods that can help to ensure the safe and efficient operation of industrial facilities. These include the use of standardized wiring methods and materials, the use of trained and qualified personnel, and the use of regular maintenance and inspection. It's also important to consider the specific requirements of the facility, including the level of protection required, the flexibility and ease of installation, and the overall cost and feasibility of the project. By considering these factors and using best practices for wiring methods, industrial facilities can ensure the safe and efficient operation of their electrical systems, which is essential for maintaining productivity and competitiveness in today's fast-paced industrial environment. Also, it's worth mentioning that, the instalation of wiring systems should be done by profesional and experiened electricians, this will ensure that the job is done corectly and safely.
Conclusion
In conclusion, wiring methods for industrial facilities are a crucial aspect of ensuring the safe and efficient operation of equipment and systems. The choice of wiring method depends on the specific requirements of the facility, and several factors should be considered, including the level of protection required, the flexibility and ease of installation, and the overall cost and feasibility of the project. By considering these factors and using best practices for cable management, maintenance, and inspection, industrial facilities can ensure the safe and efficient operation of their electrical systems, which is essential for maintaining productivity and competitiveness in today's fast-paced industrial environment. The use of modern wiring methods, such as conduit and cable, busways, and cable trays, can help to improve the reliability and efficiency of industrial facilities, and reduce the risk of electrical accidents and equipment failures. Overall, the importance of wiring methods for industrial facilities cannot be overstated, and it's essential that facilties take the time to carefully consider their options and choose the best wiring method for their specific needs.